On July 28, GE Gas Power announced that they have received funding from the US Department of Energy’s (DOE) Advanced Research Projects Agency-Energy (ARPA-E) to advance two projects related to new gas turbine technologies. The DOE has bestowed $4.2 million to accelerate GE’s research on how to lower carbon emissions from gas turbines. The funding is in line with the energy goals set by the federal government.
Last December, the US President signed an executive order to make the federal government carbon neutral by 2050. In connection to this, in May 2022, the DOE announced that it will invest $38 million to decarbonize four of its national laboratories and aim to achieve net zero greenhouse gas emissions no later than 2050.
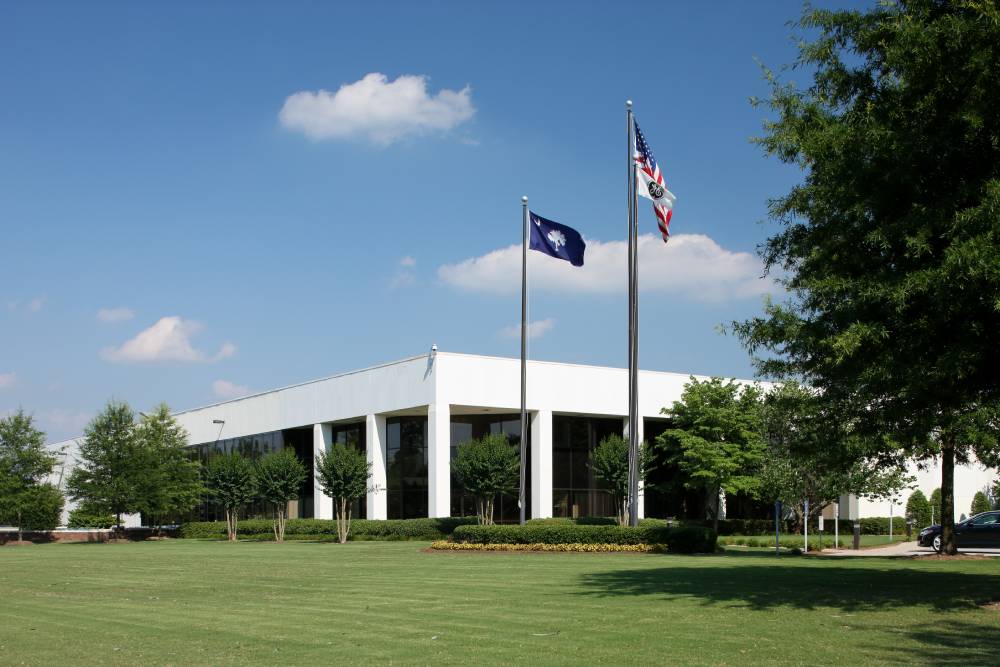
GE Gas Turbine Technology
The federal funding comes specifically from the ARPA-E OPEN 2021 program that supports technologies working towards a decarbonized energy system. If successful, the ARPA-E- funded research will be able to accomplish energy goals by bringing greater efficiency to existing systems and reducing the energy required to build turbines.
GE’s two projects are “lifted-flame combustion for high-hydrogen reheat gas turbines” and “manufacturing high-yield investment castings with minimal energy.” Both initiatives will be undertaken by GE at its Gas Turbine Technology Center in Greenville, South Carolina, which is home to the world’s largest gas turbine manufacturing facility and full-scale combustion test facility. Foundational testing for the new technology will be carried out at Georgia Atlanta-based Georgia Institute for Technology, a university which specializes in engineering and gas turbine combustion.
In a written statement, John Intile, Vice President, Engineering at GE Power said, “As one of the world’s leaders in combustion technology, GE Gas Power is leading technology and manufacturing advancements in the power generation industry to enable low or zero-carbon power generation, all of which fundamentally relies on conducting advanced research both at GE and with collaborators.” He mentioned that they he is pleased the DOE has recognized the need for alternative methods to boost the efficiency of gas turbines. Intile added, “We look forward to developing these breakthrough technologies with prestigious collaborators, including Georgia Institute of Technology (Georgia Tech), our GE Global Research Center, and DDM Systems, a pioneering company in the investment casting industry.”
Lifted-Flame Combustion for High-Hydrogen Reheat Gas Turbines
Tim Lieuwen, Regents’ Professor and Executive Director of the Strategic Energy Institute at Georgia Tech expressed his delight at being able to collaborate with two industry leaders. He admitted that they will be working to deploy cutting-edge diagnostic and modeling tools that will “predict key hydrogen flame parameters and those relating to macro-engine performance.”
The new technology will target net plant efficiencies of 67% of greater on a wide range of fuel compositions, while meeting strict emission standards. The goal is to increasing gas turbine combined cycle plant efficiency by five or more percentage points in the next decade sot that GE can easily transition to cleaner energy models
The DOE is committed to slashing carbon pollution across industries from manufacturing to construction. The mission is to mitigate the effects of climate change and lower energy costs while supporting technologies with clean energy.
Manufacturing High-Yield Investment Castings With Minimal Energy
The second project will focus on developing casting technology including innovative furnace development and 3D printed additive ceramic mold technologies that will fundamentally change the production of high-value metal components for gas turbines. The new system could produce cast parts using 90% less energy than traditional methods without compromising on quality, while improving yield and consistency.
Tom Amond, Emerging Technology Incubator at GE Gas Power revealed, “the proposed system of technologies, combining digital tooling, cutting edge additive ceramic mold printing, and lean flow casting technology, will enable us to respond rapidly while reducing our energy usage and carbon footprint.” GE Gas Power will collaborate with DDM Systems that offers #D pritign technologies for investment casting.
Together, both the projects will help improve the efficiency of GE’s gas turbines while bringing down energy costs for a cleaner world. Over 90 companies and organizations have joined the DOE’s “Better Climate Challenge” and pledged to reduce their carbon emissions by 50% by 2030 and to promote clean energy.